Understanding Precision Injection Molding: A Guide for Metal Fabricators
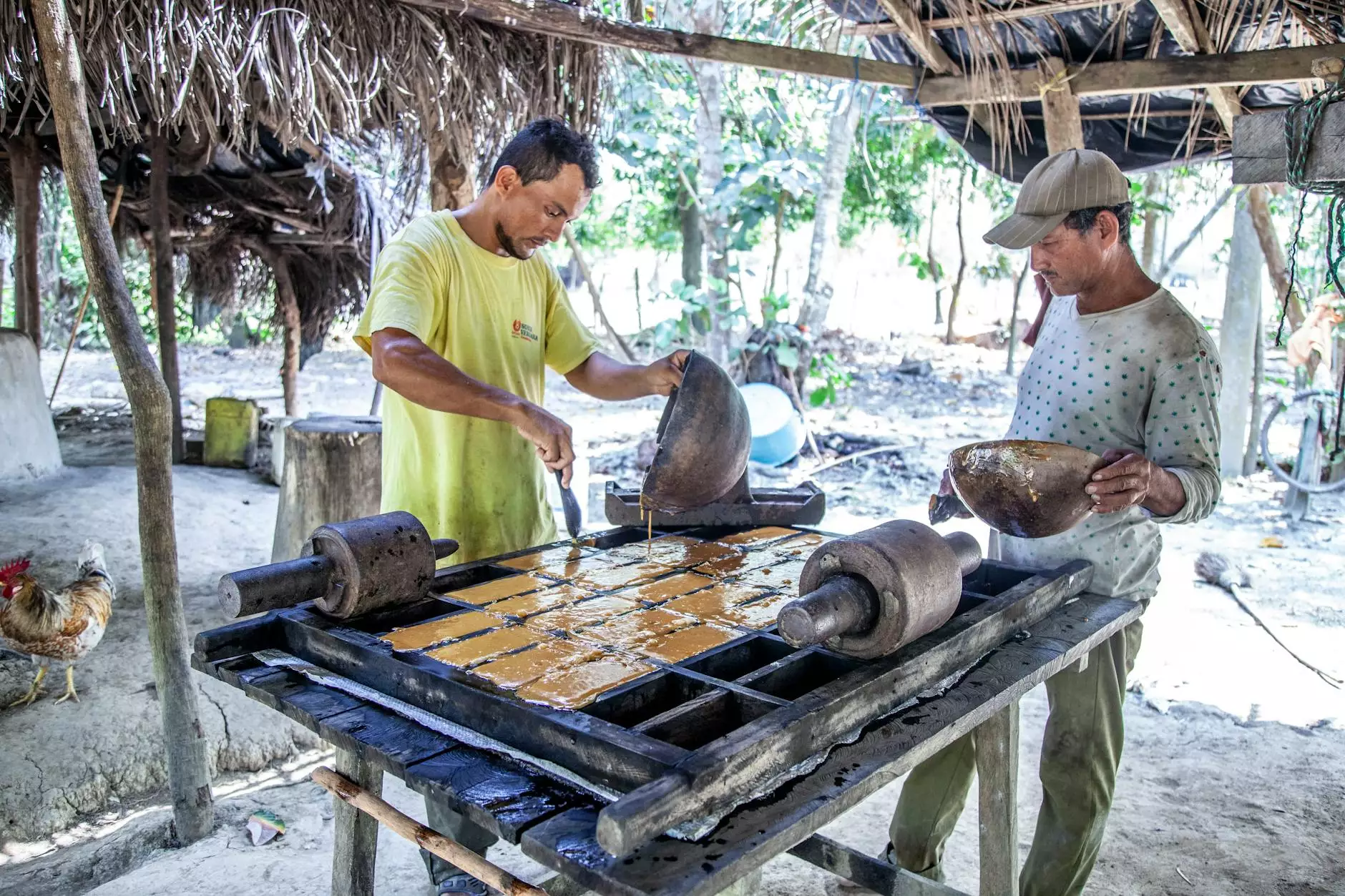
Precision injection molding is a state-of-the-art manufacturing process that has revolutionized the production of complex parts, particularly in the field of metal fabrication. This method allows for the creation of parts that are not only accurate and consistent but also cost-effective and efficient. As the demand for high-quality components continues to rise, understanding precision injection molding becomes essential for businesses in the metal fabrication sector.
What is Precision Injection Molding?
At its core, precision injection molding is a specialized process used to manufacture parts by injecting molten material into a mold. The mold is designed to create a specific shape, allowing for the production of intricate and detailed components. This technique is primarily used with thermoplastics but is increasingly utilized for metals and metal alloys.
The Process of Precision Injection Molding
The process can be broken down into several key stages:
- Material Selection: The choice of material is critical. Thermoplastics, such as ABS, polycarbonate, and nylon, are commonly used materials. However, advancements have allowed for the injection of certain metals and composite materials, expanding the versatility of this technique.
- Mold Design: An effective mold design is crucial for the success of the injection molding process. Engineers utilize CAD software to create precise blueprints that encompass all necessary dimensions and cavity details.
- Melting the Material: The selected material is heated until it melts, becoming viscous enough to flow into the mold cavity.
- Injection Phase: Using a high-pressure injection unit, the molten material is injected into the mold. This phase requires careful control of temperature and pressure to ensure the material fills the mold entirely without defects.
- Cooling and Solidification: The injected material cools and solidifies within the mold, taking the shape of the desired component.
- Mold Opening and Part Removal: Once the material has cooled sufficiently, the mold is opened, and the finished part is ejected. Additional finishing processes may be required to achieve the desired specifications.
Benefits of Precision Injection Molding
Utilizing precision injection molding offers numerous advantages, particularly for businesses operating within the metal fabrication industry. Here, we outline the key benefits:
1. High Precision and Accuracy
One of the most significant advantages of precision injection molding is its ability to produce parts with exceptional accuracy. This level of precision is essential for components that must fit together seamlessly, ensuring the final product meets stringent quality standards.
2. Consistency and Reproducibility
Once a mold is created, the injection molding process yields consistent results across large production runs. This consistency reduces the likelihood of defects, saves time on production, and enhances overall productivity.
3. Cost-Effectiveness
Although the initial investment in mold design and manufacturing can be high, the cost per part decreases significantly at scale. This makes precision injection molding a cost-effective solution for large production volumes.
4. Design Flexibility
Design engineers find great benefits in the flexibility offered by precision injection molding. They can create intricate designs that would be difficult or impossible to achieve with traditional machining or other manufacturing processes.
5. Material Efficiency
The precision of the injection molding process allows for efficient use of materials, minimizing waste during production. This aspect is not only cost-saving but also environmentally friendly.
Applications of Precision Injection Molding in Metal Fabrication
Precision injection molding is used across a broad spectrum of industries, notably:
- Automotive Industry: Parts such as housing, connectors, and interior components benefit from the durability and precision of injection molding.
- Aerospace: The aerospace industry demands lightweight and high-strength components, making injection-molded parts ideal for meeting these requirements.
- Medical Devices: The production of precise medical instruments and devices relies heavily on the accuracy and reliability of injection molding.
- Consumer Electronics: Many components in electronics, such as enclosures and internal parts, are produced using this method because of the intricate design possibilities.
Choosing the Right Partner for Precision Injection Molding
For businesses seeking to enhance their manufacturing processes, selecting the right partner for precision injection molding is critical. Here are key factors to consider when choosing a provider:
1. Experience and Expertise
Look for manufacturers with a solid track record in precision injection molding. Experienced partners will have the knowledge and skills necessary to produce high-quality parts that meet or exceed industry standards.
2. Technological Capabilities
Advanced technologies such as 3D printing for mold design and state-of-the-art injection molding machines can significantly influence the quality and efficiency of production. Ensure your partner is equipped with the latest technologies.
3. Material Options
Different projects may require various materials. A versatile partner with access to a broad selection of materials, including specialized thermoplastics and metal options, can accommodate diverse project needs.
4. Quality Assurance Processes
Quality control should be a top priority, ensuring that all parts produced meet strict specifications. Ensure that your partner has established quality assurance protocols in place.
5. Customer Support
Effective communication and support throughout the process from concept to delivery are vital. Choose a partner that values customer relationships and is proactive in addressing concerns.
DeepMould.net: Your Go-To Source for Precision Injection Molding
At DeepMould.net, we pride ourselves on being leaders in the field of precision injection molding. With years of experience, cutting-edge technology, and a commitment to quality, we have established ourselves as a trusted partner for metal fabricators and other industries. Our specialized team is dedicated to understanding the unique needs of each client, ensuring that every solution we provide is tailored to their specific requirements.
Why Choose DeepMould?
- Custom Solutions: Our team collaborates closely with clients to develop molded parts that align with their exact specifications.
- Rapid Prototyping: We offer rapid prototyping services to help clients visualize and test their designs quickly and effectively.
- Competitive Pricing: We strive to offer competitive pricing without compromising on quality.
- Sustainability: Our processes are designed to minimize waste, promoting sustainable manufacturing practices.
Conclusion
In conclusion, precision injection molding stands as a cornerstone of modern manufacturing, particularly within the metal fabrication industry. Its myriad benefits, including high precision, cost-effectiveness, and design flexibility, make it an indispensable process for producing high-quality components. By choosing an experienced and technologically advanced partner like DeepMould.net, businesses can ensure they remain competitive and capable of meeting the evolving demands of the market.
Whether you are looking to manufacture automotive parts, precise medical devices, or intricate consumer electronics, understanding the value and application of precision injection molding will position your business for success. Partner with us for innovative solutions that cater to your fabrication needs.